A shot blaster machine is an industrial surface preparation tool designed to clean, strengthen, and prepare surfaces by shooting abrasive materials (like steel shots or grit) at high speed. This process removes rust, old coatings, or dirt and creates a textured surface that allows paint, coatings, or adhesives to bond more effectively. It’s fast, efficient, and eco-friendly, making it a go-to solution for industries like manufacturing, construction, and automotive.
A shot blaster machine is the modern solution to these problems. This powerful tool revolutionizes surface treatment by providing a faster, more consistent, and eco-friendly way to clean and prepare surfaces for coatings or other applications. But what exactly is it, how does it work, and why is it essential for your business? Let’s dive in.
This machine is widely used in industries such as manufacturing, construction, and automotive. Its primary functions include:
- Removing rust, scale, and old coatings.
- Preparing surfaces for painting, coating, or bonding.
- Enhancing the durability of metal parts through a process called shot peening.
By creating a clean, roughened surface, a shot blaster machine ensures better adhesion for coatings and improves the overall quality of the final product.
How Does a Shot Blaster Machine Work?
Here’s a simple breakdown of how a shot blaster machine operates:
- Loading Abrasive Media: Steel shots, grit, or other abrasive materials are loaded into the machine.
- Propulsion Mechanism: A high-speed wheel or compressed air propels the abrasives onto the target surface.
- Impact Process: The abrasives hit the surface, removing dirt, rust, or old coatings, and creating a textured finish.
- Abrasive Recovery: Used abrasives are collected, cleaned, and recycled for continuous use.
This streamlined process ensures high efficiency and reduces waste, making it an economical choice for large-scale operations.
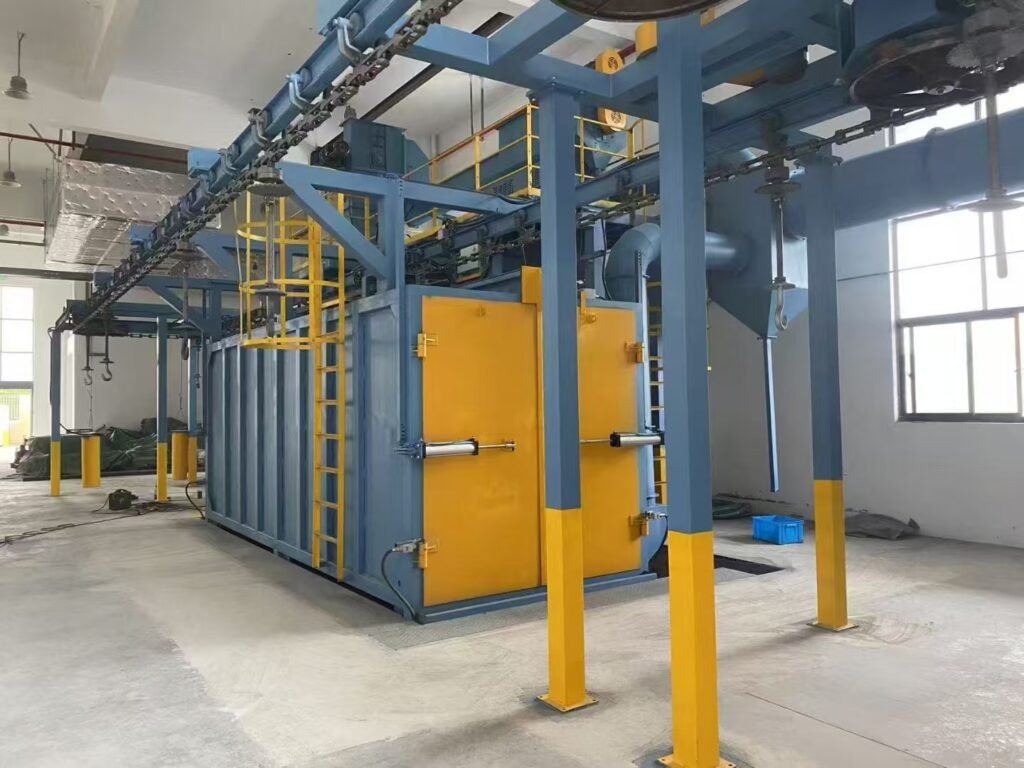
The System Behind the Shot Blaster Machine
A shot blaster machine is not just a simple device; it’s a well-engineered system with several key components working together. Each part plays a vital role in achieving excellent results:
1. Blasting Chamber: The Core of the Machine
The blasting chamber is where the action happens. This enclosed space is built to withstand the intense forces generated during the blasting process. Typically made from wear-resistant materials like manganese steel, the chamber is lined with replaceable protective plates to enhance durability.
- Functionality: The chamber contains the workpiece and confines the abrasive media, ensuring a controlled and efficient cleaning or preparation process.
- Design Features: Noise reduction measures and sealing mechanisms are incorporated to create a safer and quieter working environment.
2. Abrasive Propulsion System: The Driving Force
The abrasive propulsion system is the heart of the shot blaster machine. It propels abrasive media at high speeds onto the surface of the workpiece. There are two primary propulsion mechanisms:
- Centrifugal Wheel System: A high-speed wheel spins at thousands of revolutions per minute, throwing abrasives outward using centrifugal force. This method is ideal for high-volume applications due to its efficiency and precision.
- Compressed Air System: In smaller or portable machines, compressed air is used to propel abrasives. This system offers greater flexibility and is perfect for detailed or localized cleaning tasks.
Both systems are designed to deliver abrasives with maximum energy and precision, ensuring effective surface treatment without damaging the material underneath.
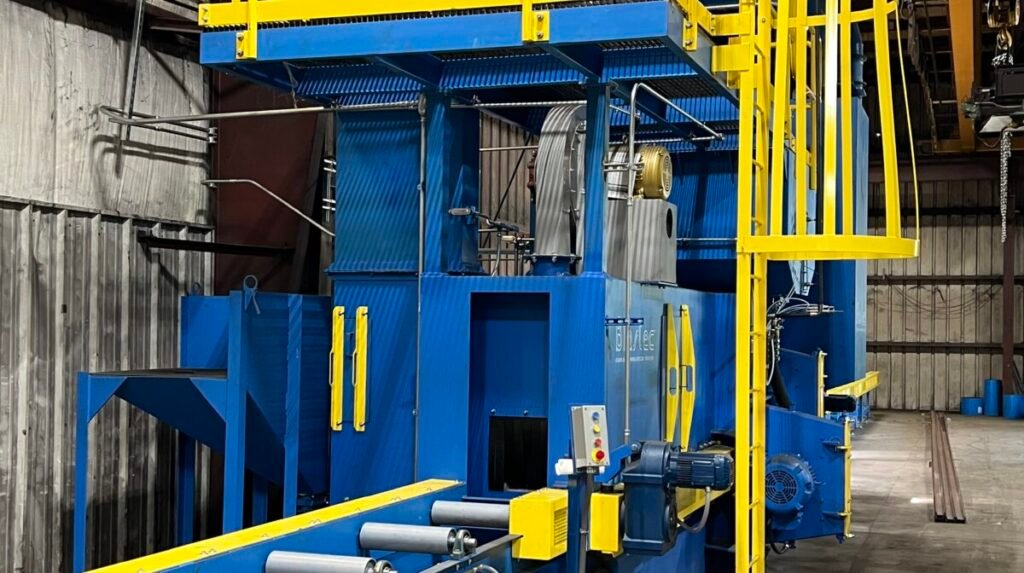
3. Abrasive Recovery and Separation System: Sustainability in Action
A critical feature of any shot blaster machine is its ability to recover and recycle abrasives. This system ensures that the abrasives are used efficiently while maintaining a clean workspace.
- Abrasive Recovery: A combination of conveyors, elevators, and hoppers collects spent abrasives from the blasting chamber.
- Separation System: Advanced separation mechanisms, such as air classifiers and vibrating screens, remove debris, dust, and broken abrasives, ensuring that only clean, reusable materials are sent back into the process.
This system minimizes waste, reduces operating costs, and ensures consistent blasting quality.
4. Dust Collection System: Keeping It Clean
The dust collection system is essential for maintaining a safe and environmentally friendly workspace. During the blasting process, fine particles and dust are generated, which need to be effectively captured and filtered.
- Features: This system typically includes high-efficiency filters and cyclonic separators to trap and contain dust particles.
- Benefits: By reducing airborne contaminants, it protects workers' health, improves visibility in the work area, and ensures compliance with environmental regulations.
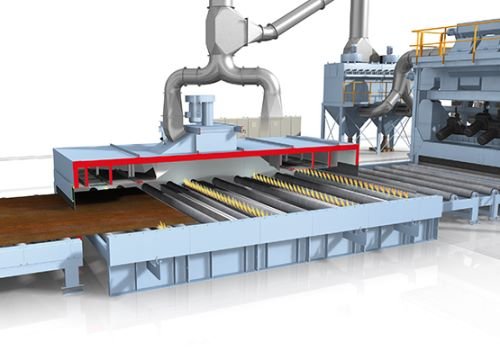
5. Workpiece Handling System: Precision and Versatility
The workpiece handling system ensures that the components being treated are moved smoothly and uniformly through the blasting process. The type of handling system varies based on the machine design and application:
- Tumble Belt: Ideal for bulk cleaning of small parts, where the belt rotates to expose all surfaces evenly.
- Hanger Type: Designed for large or irregularly shaped parts that are suspended and rotated for thorough cleaning.
- Roller Conveyor: Used for long and flat components like pipes and beams, where the conveyor feeds the workpiece through the blasting chamber.
This system ensures that each surface is treated consistently, regardless of the component's shape or size.
6. Abrasive Storage and Feeding System: Continuous Operation
To keep the machine running efficiently, the abrasive storage and feeding system ensures a steady supply of abrasive media. Key features include:
- Storage Hopper: Holds a large volume of abrasives, ready for use.
- Automatic Feeding Mechanism: Delivers the right amount of abrasive to the propulsion system, ensuring consistent blasting intensity.
This system minimizes downtime and allows for uninterrupted operation during high-volume tasks.
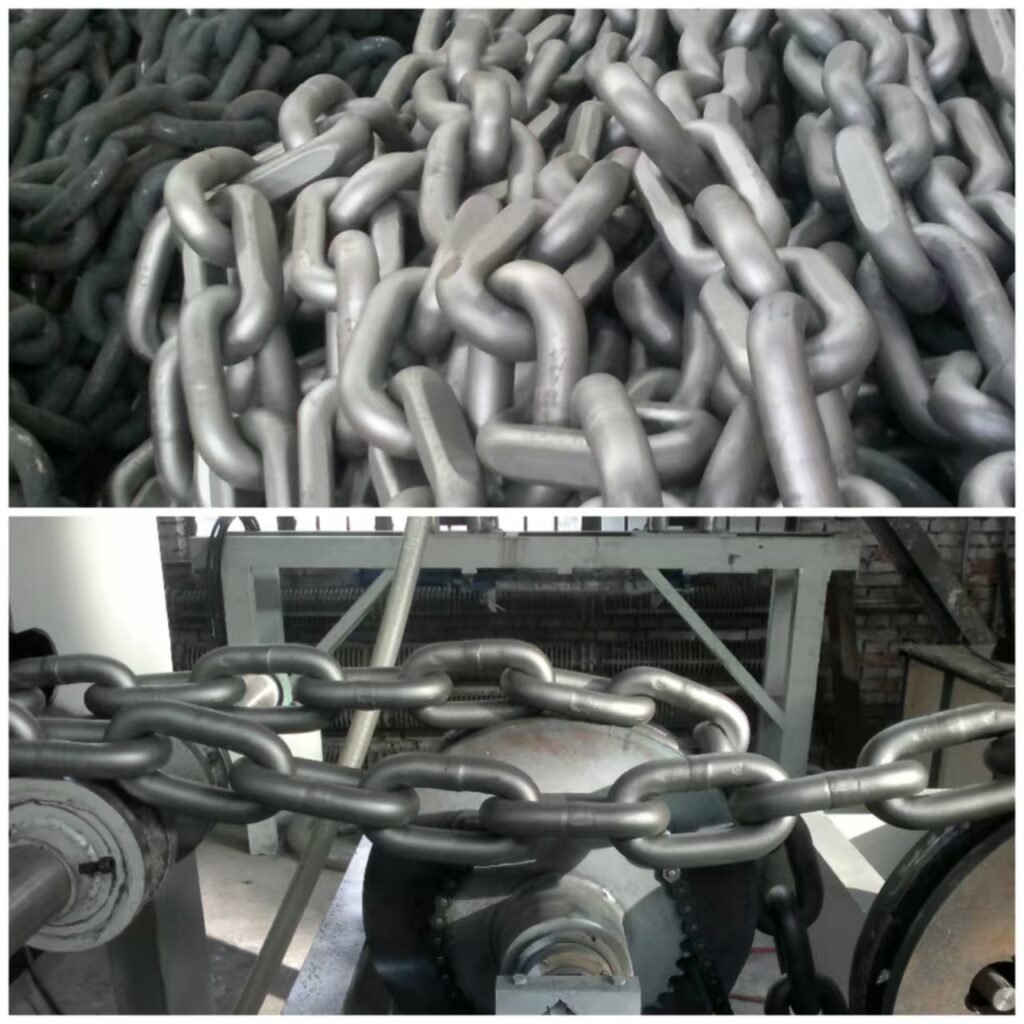
7. Control System: The Brain of the Machine
Modern shot blaster machines are equipped with advanced control systems that make operation intuitive and precise. These systems include:
Monitoring Tools: Real-time data on machine performance and abrasive usage helps optimize productivity.
Programmable Logic Controllers (PLCs): Allow operators to set parameters like blasting speed, intensity, and duration.
Safety Features: Automated shutdowns, alarms, and maintenance reminders ensure safe and reliable operation.
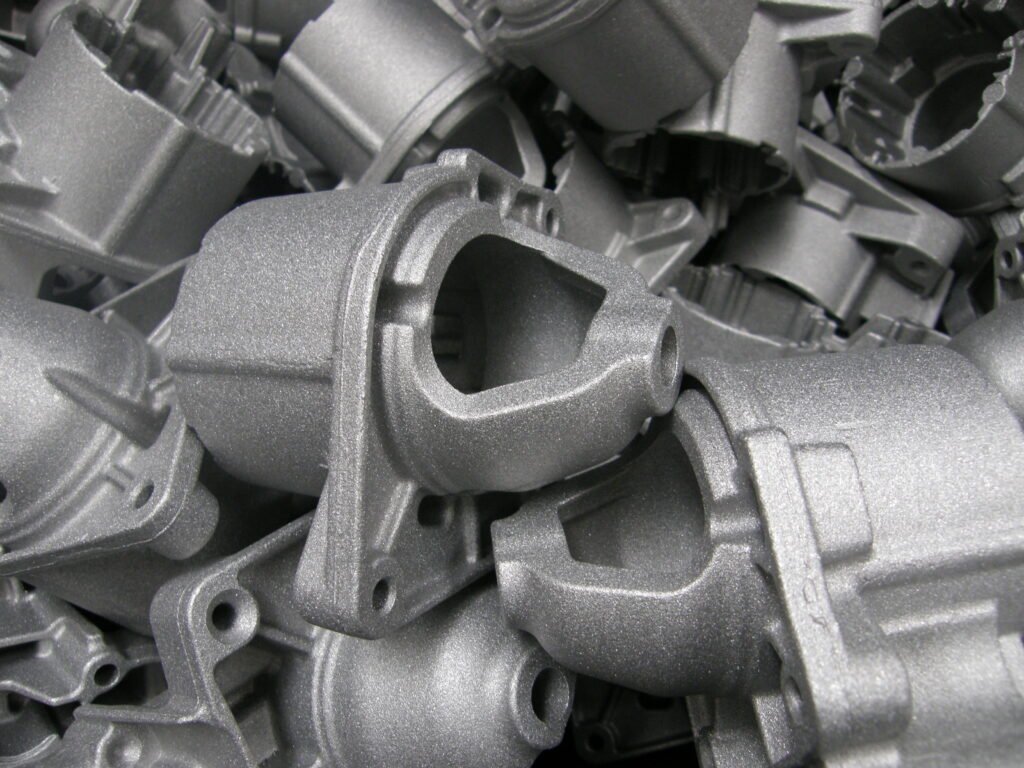
Advantages of a Shot Blaster Machine
Using a shot blaster machine offers numerous benefits:
- Time-Saving
The automated process is much faster than manual cleaning methods, saving valuable time in industrial operations. - Consistent Results
Unlike manual methods, a shot blaster machine provides uniform cleaning and surface preparation, ensuring high-quality results every time. - Eco-Friendly
The use of recyclable abrasives and dust collection systems reduces environmental impact, making it a sustainable choice. - Cost-Effective
By reducing labor requirements and recycling abrasive materials, shot blaster machines lower operational costs. - Versatility
These machines can handle various materials, from metal to concrete, and adapt to different sizes and shapes of workpieces.
Applications of a Shot Blaster Machin
Shot blaster machines are used in a variety of industries for tasks such as:
- Metal Surface Cleaning: Removing rust, scale, and old coatings from steel and other metals.
- Concrete Preparation: Roughening concrete surfaces for better bonding of coatings or overlays.
- Pipeline Maintenance: Cleaning the inner and outer surfaces of pipes to prevent corrosion.
- Shot Peening: Enhancing the strength and durability of metal components like gears and springs.
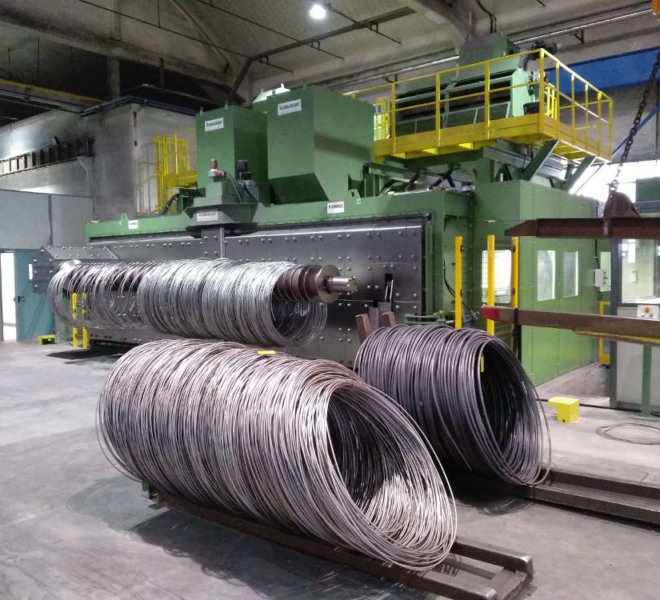
Why Choose a Shot Blaster Machine?
If you’re in an industry that requires surface preparation, investing in a shot blaster machine is a smart choice. Here’s why:
- It eliminates manual labor and speeds up the cleaning process.
- It provides better results, ensuring surfaces are clean, uniform, and ready for coating or bonding.
- It reduces waste and complies with environmental standards.
Our company offers high-quality shot blaster machines tailored to your needs. With advanced technology, durable construction, and excellent after-sales support, our machines are designed to enhance your productivity and improve your bottom line.
Conclusion: Transform Your Operations
A shot blaster machine is more than just a tool; it’s a transformative solution for businesses looking to improve surface preparation processes. By investing in this technology, you can save time, reduce costs, and achieve superior results.
Contact us today to learn more about our shot blaster machines and how they can benefit your business. Let’s work together to take your operations to the next level!