If you're involved in industrial surface preparation, you've likely heard of grit blasting machines. But what exactly is a grit blaster, and why is it so crucial for cleaning, smoothing, and preparing surfaces? In this article, we’ll break down what grit blasting is and how it benefits various industries.
A grit blaster, also known as sandblasting or abrasive blasting, is a powerful machine used for cleaning and preparing surfaces by propelling abrasive materials at high speeds. It’s used in industries like construction, automotive, and metalworking to remove rust, paint, and contaminants, or to etch and smooth surfaces.
Now, let’s dive into how a grit blaster works and where it’s used across different industries.
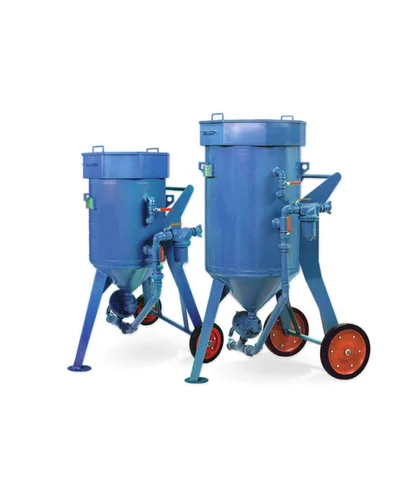
1. What is a Grit Blaster?
A grit blaster is a type of abrasive blasting machine that uses high-pressure air to propel abrasive materials—often called grit—at surfaces to clean, smooth, or prepare them for further treatment. The grit used can vary, but it usually includes sand, steel shot, or aluminum oxide. This blasting process is often referred to as sandblasting, though sand is just one type of abrasive.
- How It Works: The abrasive grit is stored in a pressure vessel and then directed toward a surface using compressed air. The grit impacts the surface at high velocity, removing contaminants, rust, old coatings, or imperfections, depending on the job at hand.
- Main Components: A typical grit blaster setup includes the abrasive material, pressure tank, blast hose, and nozzle.
Tip: Grit blasters can be adjusted to use different types of abrasives and varying pressure levels, making them adaptable for various cleaning and surface preparation tasks.
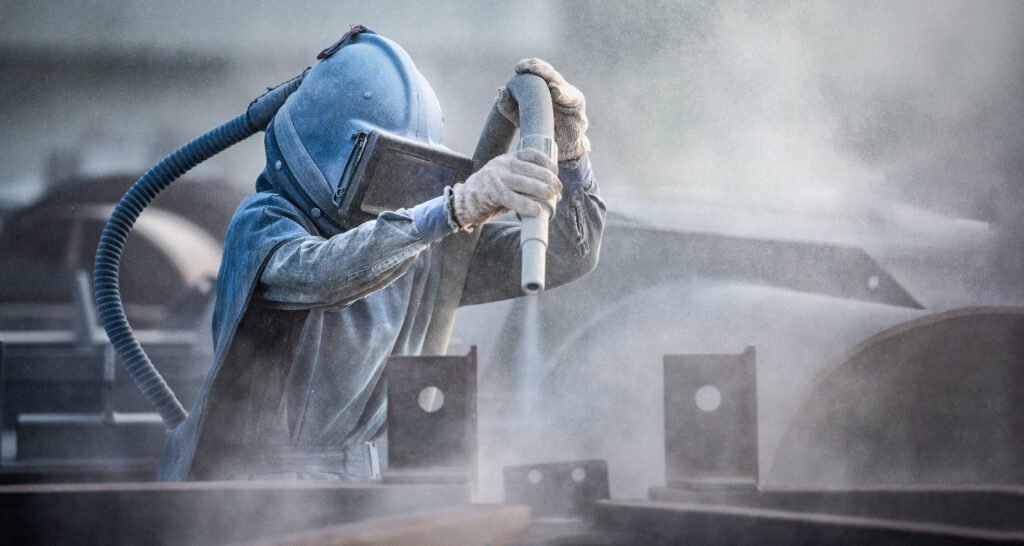
2. Applications of Grit Blasters
Grit blasting is used across a range of industries to prepare surfaces for further processing. It is particularly effective at cleaning tough materials and improving surface finish.
- Construction Industry: Grit blasters are used to clean concrete surfaces, remove old paint from steel beams, or prepare surfaces for coating and sealing.
- Automotive Industry: In the automotive sector, grit blasters are used to clean car parts, including engine components, brake parts, and chassis. They are especially useful in removing rust or preparing surfaces for painting.
- Metalworking and Fabrication: Metal parts such as castings, welds, and structural components often need grit blasting to remove contaminants like scale, rust, or oils before coating or further processing.
- Shipbuilding: Large metal components like ship hulls often undergo grit blasting to remove corrosion, prepare surfaces for coatings, and ensure long-term durability in harsh marine environments.
Tip: Grit blasters are essential for improving adhesion during coating or painting, as a clean, roughened surface allows for better bonding between the material and the coating.
3. Types of Abrasives Used in Grit Blasting
The type of grit used in the blasting process varies depending on the job. Different abrasives are selected based on their hardness, size, and shape to achieve the desired effect.
- Silica Sand: This is the most traditional abrasive, used for general-purpose cleaning and surface preparation. However, due to health risks associated with silica dust, many industries have moved toward safer alternatives.
- Steel Shot or Steel Grit: Steel abrasives are typically used for cleaning metal surfaces and are known for their durability and effectiveness in removing rust or scale.
- Aluminum Oxide: Known for its hardness, this abrasive is used for finer finishing, especially on harder materials like stainless steel or alloys.
- Glass Beads: Used for more delicate blasting tasks, glass beads are often employed to achieve a smoother, more polished finish without damaging the underlying material.
Tip: Choosing the right abrasive is crucial for ensuring the effectiveness and safety of the grit blasting process. Always consider the material being blasted and the desired finish.
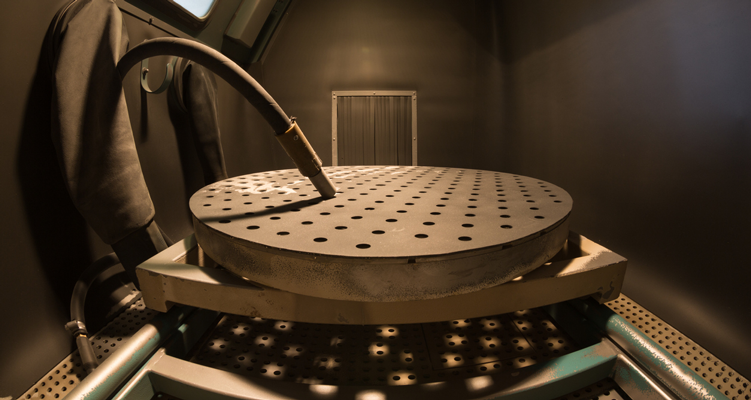
4. Benefits of Using a Grit Blaster
- Speed and Efficiency: Grit blasters can clean large surface areas quickly, making them ideal for industrial-scale operations. Compared to manual cleaning methods, grit blasting offers a much faster and more efficient way to prepare surfaces.
- Versatility: Grit blasting can be used on a wide range of materials, including metals, concrete, wood, and stone. It is effective at removing rust, old paint, grease, and other contaminants.
- Improved Surface Quality: Grit blasting can provide a roughened surface ideal for paint or coating adhesion, improving the longevity and durability of the final product.
- Cost-Effective: Using a grit blaster reduces the need for extensive manual labor, which can save both time and money in the long term.
Tip: By investing in a high-quality grit blaster, companies can enhance productivity, reduce downtime, and achieve higher-quality surface finishes at a fraction of the cost of manual labor.
5. Safety Considerations When Using a Grit Blaster
While grit blasting is highly effective, it’s important to consider safety. The high-pressure process can create dust and flying debris, so appropriate safety measures must be taken to protect workers.
- Protective Gear: Operators should wear safety goggles, gloves, and respiratory protection to prevent injury from flying particles or inhaling abrasive dust.
- Ventilation: Adequate ventilation is essential to ensure that dust and particles are properly managed, especially when using abrasive materials like silica sand.
- Proper Training: Workers should be trained on the safe operation of grit blasters, ensuring they understand how to handle the equipment and avoid accidents.
Tip: Implementing strict safety protocols and using dust collection systems can greatly reduce health risks associated with grit blasting.
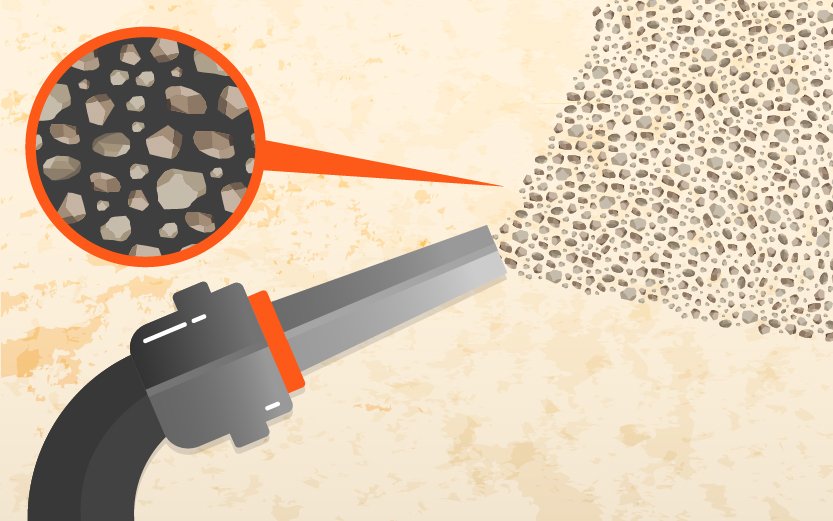
Conclusion
A grit blaster is an essential tool for industries that require high-quality surface cleaning and preparation. Whether you’re in construction, automotive, metalworking, or shipbuilding, a grit blaster can save time, reduce labor costs, and ensure that surfaces are properly prepped for further treatment or finishing. By understanding the process and selecting the right abrasive for the job, you can significantly improve the efficiency and quality of your operations.
Tip: When choosing a grit blaster, make sure to consider the scale of your operation and the type of materials you’ll be working with to ensure you select the best equipment for your needs.